Kelly: Today we have Jackie Evans with us to talk about her experience with Passive House. Jackie works with NRB Modular's Affordable Housing Department, and we have had the pleasure of working with NRB on the King William Passive House project in Hamilton, Ontario, which is partly funded by the Rapid Housing Initiative.
So today we're gonna discuss with Jackie how the King William Project in Hamilton has opened an avenue for modular construction and Passive House. We're gonna also get into connection with the Federal Incentive Funding for Affordable Housing, which means high-performance energy standards like Passive House and what it means to build modular.
As we learn more about her experience and career, we will dive into what makes modular construction and Passive House uniquely aligned. And we're gonna also hear about Jackie's experience with group Passive House training the NRB Modular team received from Peel Passive House at the onset of the King William Passive House project.
So welcome and thanks for joining us today, Jackie. We appreciate
taking the time outta your day.
Jackie: Happy to be here.
Kelly: Oh, that's fantastic to hear. So we're just gonna start with a bit of some icebreaker questions. Get everybody feeling a little bit more loose, a little less anxious, a little less kind of nervous.
And one that I always find that people get a kick out of is what would your parents say you do for a living?
Jackie: I don't think my parents have ever understood what I did for a living from the time I graduated from design school. They just know that I am involved in the housing sector. That's really all they know. They don't really know what I do. Yeah, very big-picture stuff.
Kelly: So maybe you can share with our listeners before we get into a bit more about, what it is that NRB does, but maybe you can share with us who you are and what you do with NRB and maybe get into kind of maybe your experience and your understanding of sustainability and construction.
Jackie: Sure. I'm in the latter stages of my career now. So I have a long and storied past. I actually graduated from interior design at Ryerson many years ago. Shortly after that I actually went into sales and worked for Interface Flooring Systems. So most people that know anything about sustainability know a little bit about Interface.
They're known as the manufacturer that started on the road to sustainable manufacturing many years ago. Trying to get to zero and then restorative. So in Canada, I was in their sales division and then I moved partially into a role that was specific to the environmental side of the business.
I was on the first board of directors for the Canada Green Building Council. So I used to hang out with all the, what I would say, grandfathers of sustainability. The Peter Busby's, Joe Van Bellingham, Ray Cole, all those guys. Bob Bates from an energy perspective. And I was the person in the background just trying to be, "have you thought about what the manufacturers are gonna say about this?"
So that was my role. And so I'm thrilled to be now at NRB. I've been here for about uh, 18 months and really am enjoying getting involved in the manufacturing side again, but specifically on a much larger scale and around housing. That's kind of what I do.
Kelly: That's fairly interesting. I hadn't realized you were on the CGBC Council
Jackie: that's, that was a long time ago and I was deeply involved.
Kelly: That's a surprise.
Jackie: Yeah. So I was more on the interior side yeah I brought the Canadian version of LEED CI into Canada.
Kelly: That's cool. Was there anything from that experience earlier on in your career that kind of inspired you to, to how you've progressed with NRB Modular and then like any connections you can make back from that experience and what impacted you most from that, that you brought to NRB?
Jackie: Yeah, we're constantly striving, to look at better ways to build and better ways to incorporate sustainable practices into the design. So yeah, there's a lot that I bring from that experience. Even right now we're, looking at our supply chain and how we can really delve into both looking from the east side, east and west of the country.
Cause right now we have different procurement practices and we're amalgamating all of that so that we can. Buy from one supplier or two or three, but, narrow that down and really make sure that those suppliers meet our standards.
Kelly: Oh that's exciting. So I guess before we get a bit too far into this, maybe you can speak to our audience about NRB and what it is that you do as a whole.
I understand your division of Dextera but maybe speak a bit more about what NRB does.
Jackie: Yeah, we should probably explain that. Yeah, NRB is the largest modular manufacturer in Canada. We have four manufacturing plants across the country. Kamloops, Calgary, Grimsby and a new plant in Cambridge, Ontario.
The plant in Cambridge, Ontario is specific for housing. But NRBs been around for over 40 years. Primarily building in steel in Grimsby, which is where I'm located right now. And we build what we call full volumetric modular construction. So that's quite specific.
And I always like to talk to people about modular construction, and that's usually the first thing that I tell people is that we are full volumetric modular builders. We build modules that are fully complete inside and out. And then. For lack of a better term, stack 'em and pack 'em. We sling them into place.
And so they are fully finished on the inside. We joke about this, but if you want the toilet paper on the toilet roll, we can put it there. The appliances are in, if you want a TV on the wall, it's there. The mirrors in the bathroom are all installed, so it's fully finished.
Kelly: That's super cool. Yeah, I think oftentimes there is a kind of delineation. I think people get often mixed up between what modular construction is and what prefabricated is. So it's always nice to have this kind of definition of what it means to deliver modular versus what it means to deliver prefabricated.
So is there anything that you would have for me, as I don't know an explanation of the differences between the two? For the industry, cause it's often something that gets confused, I find, anyway. When you're talking with architects and designers, there's this hiccup along the way where people don't seem to make the connection.
So would you have any advice for how people can better define the differences between prefab and modular?
Jackie: It is very difficult at the moment to ensure that everybody's talking the same language. And as a modular industry, we do have to get better about defining that. But I would say that typically what we do is still considered prefab.
But it's more of a complete prefab. I actually like to use the term offsite construction. That's all-encompassing, but the term modular also has some negative connotations because people tend to think of modular construction as being somehow a lesser form of construction, and in fact, it is not.
And they also somehow make that connection to, the mobile home industry, which is not even remotely related. Yeah, I, we do, Kelly, we need to get better at defining these things so that when we're talking to architects they get it.
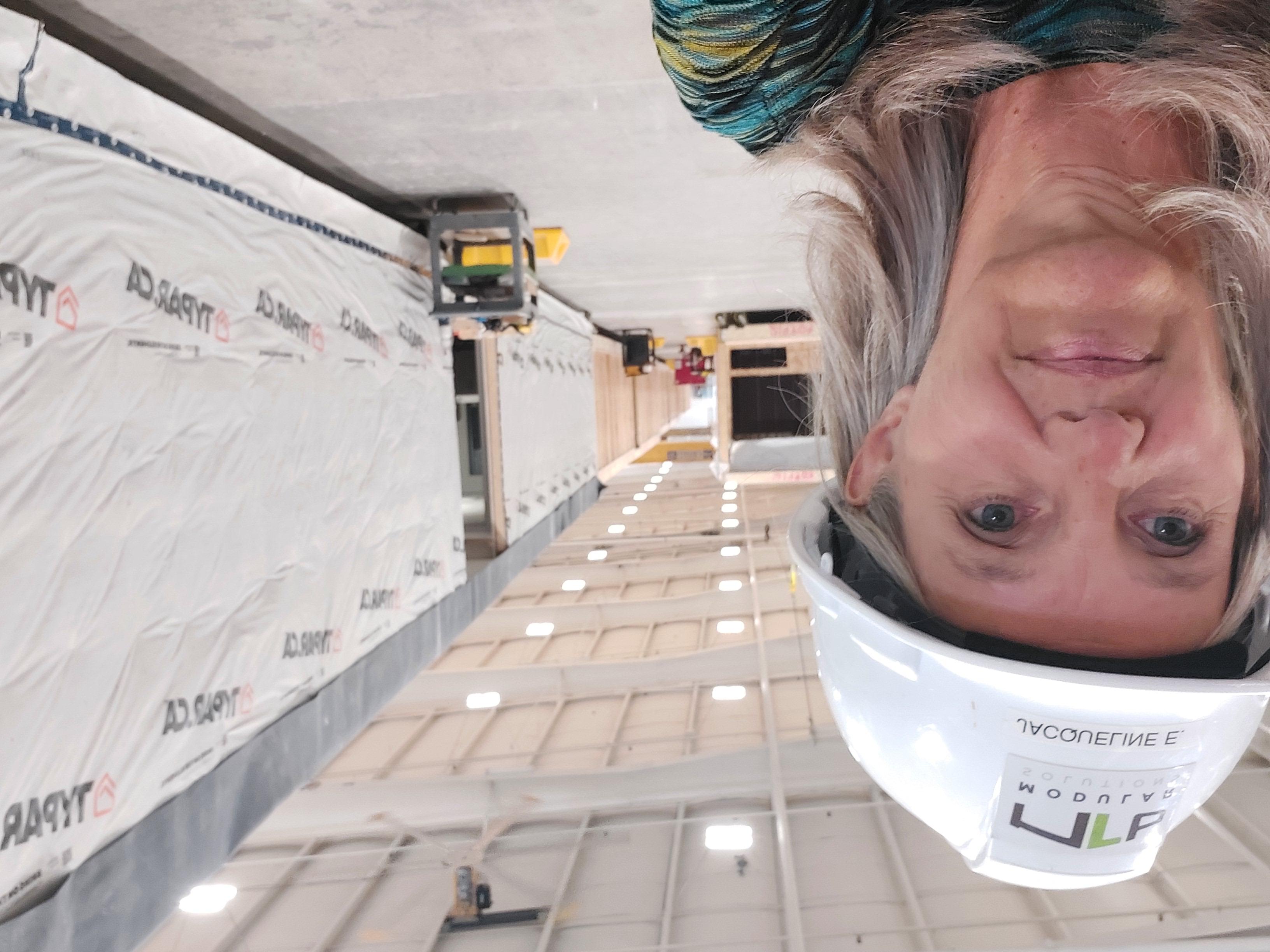
Kelly: So you just hinted there a little bit towards the industry impression of what modular construction is and how people often associate it with something that's lower quality or underbuilt or something that may not have the same longevity as something that's built in place.
Would you be able to maybe highlight any of the differences between structural integrity with modular construction compared to traditional construction? What is unique about it that lends to its impact of it or its strength of it?
Jackie: Yeah, so basically anything that you have to sling into place, crane into place, and travel long distances has to be built in a very robust way, right? So we build, in our particular case, we build full volumetric, so they're modules and we put them side to side. So you will have double walk construction and you will also have double floor and ceiling construction.
There is more material in our product than you would see in a traditional stick build. So it lends itself to a really sturdy product. And people ask me all the time, is it gonna last as long as a traditional build? And I say As long for sure, if not longer. There haven't been actual stats on that yet, but I think we're gonna get to that point where, you know, as the industry develops, we'll see comparisons between a conventional stick built and modular, specifically the volumetric.
Andrew: Yeah, I suppose you have to wait 30, 40, 50 years to really be able to do that comparison. Yeah.
Jackie: Yeah. Exactly.
Kelly: I guess NRB as a whole has been around for 40 years or so. Are there any projects built 40 years ago that you have that information on?
Are they still standing how have they held up over the years? Like anything like that you could offer.
Jackie: For sure. Most of the builds that were done in the Grimsby plant here in the east were built out of steel, so it wouldn't be a straight apples to apples to comparison.
But did a ton of retail spaces that are still standing and there are a lot of gas stations, convenience store-type things, what we call "C" stores that are still out there and you would not necessarily even know that it was modular construction. And that's really the goal is that you don't want the product to actually look modular per se.
Although there are a lot of stick-build projects out there that I look at and go, man, that looks really modular. The idea is to build with speed and to build with quality and to have a strong environmental product.
Kelly: That's super cool. So I guess you alluded a bit earlier as well that everything that gets that has to be delivered to site, whether it's being transported on a truck or what did you say, sling into place or like craned into place.
And it all has to be built a bit more robust. But could you speak a little bit more about like, how these units are transported? Are there any special considerations to be made? How does the price of transportation drive up the cost of these units? Is there anything like that, that you could speak to as well with respect to modular, getting to the site?
Because I find that's often like a bit of a standoff point for people maybe considering it because when they look at it from like an economy of scale perspective, there are all of these additional transportation costs for these large volumetric modules that, like how does that get absorbed into the project costs?
Jackie: That's a good question. And I think every project is different. Let me put that on the table. And sometimes we're transporting too far north. So we've done projects in very remote locations in the Northwest Territories to the Arctic. In those cases, you're going to places that they have very limited skilled trades and they're happy to have a full volumetric modular product show up on-site cause they don't have a lot of choices.
So those transport costs are actually absorbed fairly well into the project because the alternative is to have a large number of people come to the site and build, and that in itself is very costly because then you have to find them places to stay, et cetera, et cetera. On the flip side to that, when you're talking about more urban environments, you've got a radius in which it works.
And that's why we have plants across the country, right? So east to west. Does it always make sense to travel large distances? Not always. And those are things that we evaluate at the very beginning of the project. But it depends on the number of modules and the size of the modules. There's a lot that has to go into it.
So what typically happens is people will come to us with a project. We know the location, we map out how far we have to go. We start understanding how many mods can we ship, and, the design. That's why it's really important that we're involved very early in the early stages and that we are talking. We are either acting as the architect or we are talking directly with the architect to make sure that those mod sizes make sense for transportation because the transportation requirements across the country are actually quite different.
So in the west, we just shipped 22-foot wide mod down to Montana. They have a crazy ability to transport very large modules in the west. I think that comes from the oil and gas sector, to be honest. Having to, move very large vehicles around.
Whereas in the east we're much more restrictive. So for us, when we did the downtown Toronto projects for the city of Toronto we're on our sixth build now. That was they're, the mods are 12 and a half feet wide and 65 feet long. And those are the sweet spot for getting in and out of downtown Toronto.
Kelly: How did you determine what the sweet spot would be for getting out of downtown Toronto? It seems like a lot of logistics for all the corners you have to turn and all the big tracks to determine the widest load you could have. That's interesting. Yeah. It's
not as we do rely heavily on our transport partners to work with us to ensure that it's gonna, but yeah, sometimes.
Sometimes the shortest distance is not the way we're gonna go either. Sometimes we have to go in.
I used to always laugh at the transport of the big 50-foot, 53-foot-long trailers that would end up in downtown Toronto when I was living there. It's like, how did you get this fire into town?
And yeah. Have to make this turn. I don't understand. It's like they always look so awkward.
Andrew: It reminds me I was working in the UK in the wind sector and, you're transporting very long turbine blades, right? , and they're going to some remote locations like in Scotland and small, rural, hilly roads that are turning.
And you have to map out the entire route and say, okay, what is the pinch point? What's the road turn that's gonna limit the size of the blade and the size of the turbine? Just one little bottleneck that determines everything.
Jackie: Yeah. Most of the time we've been extremely successful and haven't had any, oops yet. I don't anticipate any. But yeah the downtown Toronto projects were tricky because of street cars too, right?
Kelly: Oh, the overhead lines. Yeah.
Jackie: There are definitely, that's why, as I said, we have to be involved right from the beginning.
Don't design modular without having your modular supplier at the table right at the beginning.
Kelly: Absolutely. Yeah. No that's intrinsic to the process. So I guess one thing that you kind of alluded to there when you were, look when you were talking about like the transportation costs and getting things to the site and you mentioned that when you're shipping to somewhat remote locations, like Northern Ontario, Northern Manitoba, or even northern parts of bc, one of the benefits, is having everything show up.
So when you're getting into these more northern and remote communities the skillset isn't there. So having, your fully finished volumetric modular construction arrive with everything that needs to do or needs to be included is a, isn't a very important benefit for those kinds of locations.
But are there any other kind of unexpected benefits to building to modern or modular construction that you could speak to? Just because I feel like that's a really good one, but I feel like there's probably more we haven't touched on.
Jackie: Yeah, there, there are. And honestly every project we find some new strange thing that we didn't really think about, right?
When we build, we have our OSB board on the inside of each one of the modules, and then we put the drywall on top of the OSB board. And that's just because it's a structural thing. , we didn't think about this, but from a bedbug perspective in the downtown Toronto projects, that turned into a real benefit.
And because it goes straight down to the floor and you can't go from unit to unit. The other thing is the sound between units is much better, so the sound transmission is lower. And we're actually trying to do some testing on that because most of the companies that do that testing are doing it on standard assemblies and don't have the double wall construction as we have.
So we have double-wall construction.
Kelly: You're double wall, you're double ceiling. Like everything. That's gotta help so much.
Jackie: Yeah. So when we transport, we have not just the double wall, but we have the insulation on the inside. And then we have tieback on the outside of that. And that is an interior wall. right? And that's, that, you just don't see that in traditional construction. So all that extra material helps for reducing the sound transmission. So there's, there are things like that and I'm sure that we are gonna continue to find things that we didn't really expect. We come up to just over a year now on the Toronto builds.
So they've been in operation for almost a year now. So I'm actually trying to get the operational numbers from the people that are actually main operating the project right now, or the building right now, so that we can look at that energy consumption and everything else because there should be because it's a better-built building.
Kelly: Absolutely.
Andrew: And does that actually include the acoustic testing you were mentioning? Is that gonna be in situ or in, in your factory or?
Jackie: We were talking about doing it in factory, but I'm not sure. It's still to be done and determined, but it's definitely something that we need to do cause we need to provide those numbers to architects to be able to give them the SEC ratings that they're looking for.
Kelly: Yeah, the SEC values are always very important to consider. So it'd be very interesting to see what's determined for that buildup. cause imagine it's very much improved over, over typical conventional construction. So that's exciting.
Jackie: Yeah, so I'm sure we're gonna find other things as we go along on our most recent builds for Toronto because the tiers are getting trickier, right? We're gonna be closer to having to produce for Passive House for the city of Toronto in the next few years, 2025, I believe. But we're already in our last two builds. There's a solar array on one and there's a green roof on the other. So that's something new for us as well, putting a green roof on our builds.
Yeah, so there are lots of good things happening.
Andrew: Does the green roof come pre-installed?
Jackie: Yeah, so this is something that I actually I haven't spoken to the operations guy about exactly how we're gonna do that.
But technically our product comes with the roof already on it, right to the site. This low-slope roof, it's already built that way into the top mod. So there's no reason why there couldn't be a lot of that groundwork done, I guess the lower levels of whatever they put on the green roof.
I'm trying to think of all those cause its layers of structure on the green roof. Yeah. So there's really no reason why we couldn't. So we might, I don't know.
Andrew: And maybe bring the birds along as well. . .
Jackie: Okay. That's pushing it. Although we did have a bird go through the plant in Cambridge the other day, we had drone footage going through the plant and a bird was flying around.
I'm like, okay. (laugh)
Andrew: Maybe you got wind that there's gonna be a green roof coming.
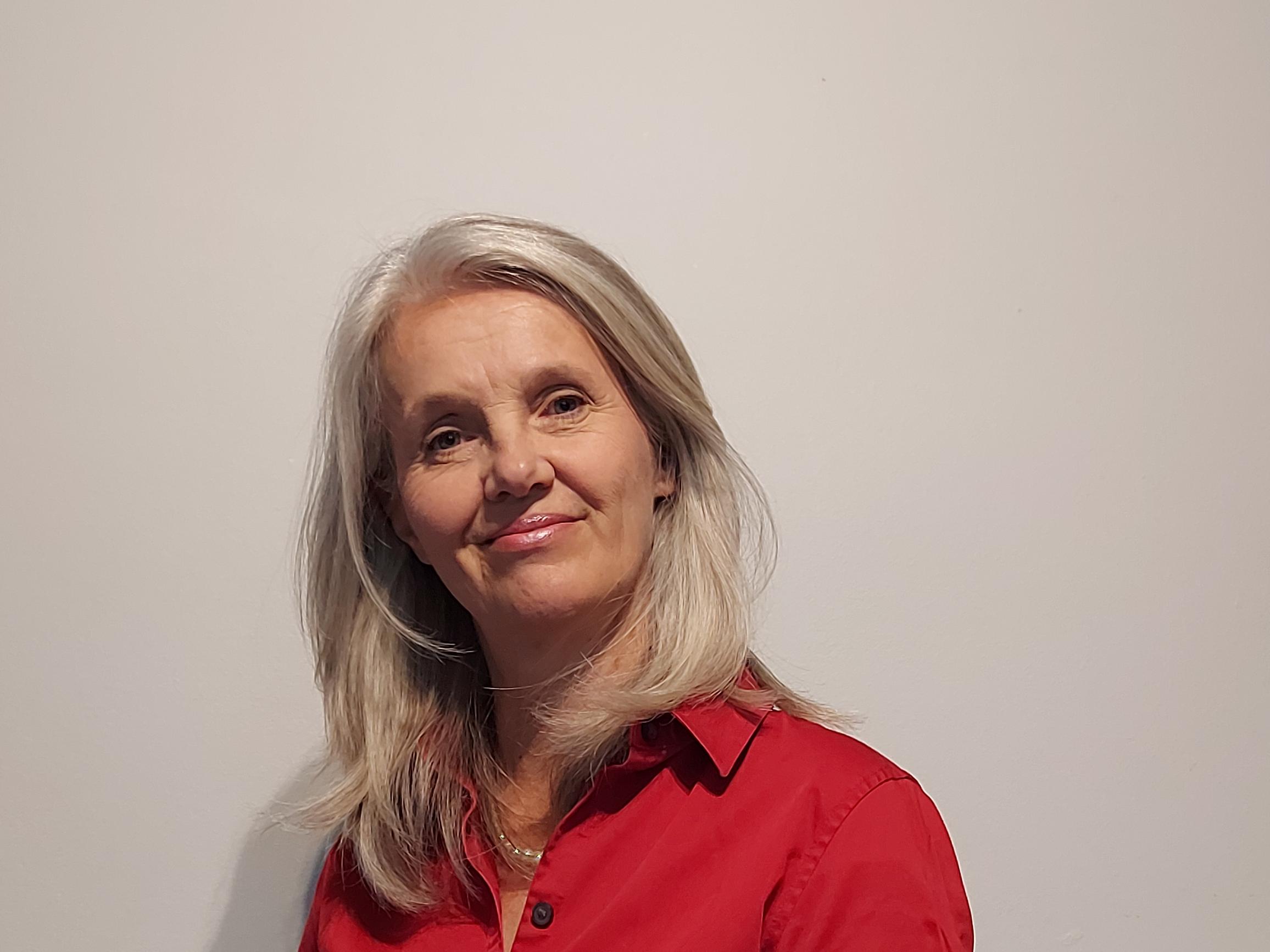
Kelly:, That's awesome. With the green roofs, I didn't realize, it'd be interesting to see if you ship them, like with the sedum layers already on. That'd be cool to see going down the highway.
Jackie: They are fully wrapped. So they are completely shrank wrapped before they leave. So there's no reason why they couldn't, why not?
Kelly: Just coming back to a bit more of the modular construction and we're looking at, designers in the industry or developers or, when you're looking for a design-build project these types of kind of structures, is there anything that developers or building owners should consider when they're looking at modular construction for the projects? Oftentimes, you hear that building prefabricated or modular, it has some restrictions, but it just depends on the team and what you're after. Is there anything that maybe you could speak to about that, like what they should be looking at or how considerations they should make?
Jackie: Yeah, so typically there really aren't really that many restrictions, but I would say honestly, that every site is different and I know that they're trying to maximize the number of square footage in the building on that site.
So sometimes we will get introduced to a project where the building is a very odd shape. That can pose some challenges for modular because, and not for, I have to be careful about how I say this because, in typical modular, it's not for housing modular where we are trying to build the exact same unit over and over and over again.
That's what we're trying to achieve. So if you have a building that's got a strange angle on it and we're not building the exact same mod over and over again, we can do that. It's just not as cost-effective. So that would be one thing like rectangular buildings are great. The other thing that I would say is the height restrictions within municipalities.
So because we are doing a floor and then a ceiling. Our buildings tend to be slightly taller overall. So if you're used to doing a steel structure a steel and concrete type building where you've got maybe a six or eight-inch concrete slab and we're gonna be more than that over four or five stories that can make a difference.
So we do need to talk about that right from the get-go is what are the height restrictions within the municipality and how can we either get a variance or how can we work within that?
Kelly: Yeah that's not a consideration I had made the additional like floor to floor height you need.
That's an interesting one.
Jackie: Yeah, we usually get around it.
Kelly: I was just gonna say aside from that one, would you think that there'd be a reason why somebody shouldn't build modular?
Jackie: Honestly, no. I think where the industry is going to go long term is going to be a hybrid because there are some restrictions in terms of height. And the height is based on the transportation, not our ability to build within the plant. Usually, our maximum height is around 13 feet, six inches from underfloor to top of ceiling. And so we'll get asked for developers who want ground floor retail with really high ceilings, like 14-foot high ceilings. And then they'll have residential above. That's when we would suggest doing a hybrid-type build. Stick, build the ground floor and then everything that is a repeatable unit above make it modular. If you think about it, so even bathroom pods or for hospitals, anywhere you, where you're building the exact same thing over and over again. Is what makes modular make sense. Or places that are so far away.
Kelly: Yeah. It adds a lot of flexibility to the design like that too. If you wanna have a unique kind of podium or an entrance level, then above that is all kinds of modular construction where it's more repeatable.
That's great flexibility.
So what are you seeing then, I guess in terms of demand, like in, in recent years? Has the demand for modular construction increased or has it just been steady across, or, are people becoming more aware of it now and wanting to include it or incorporate it as part of their projects?
Jackie: Yeah, I think the demand is there. You're seeing more modular manufacturers in the marketplace now. You saw sort of an interest in C cans for a while. We're gonna continue to see a variety of different types of modular construction. Whether they all continue to flourish is another question.
But I think that for us at NRB we know that, we have a very solid background in modular. We do a lot of different types of modular construction. Everything from kiosks to classrooms, to full schools, to as I said, c stores. So we have that solid base, and then above that, we've added the housing sector to it.
And housing is, as I said, modular is not new to us, but the housing sector is relatively new within the last five years. And that came from us doing the oil and gas sector out west and delivering staff housing in very remote locations. And that sort of morphed into BC housing. And building over 30 builds for them is affordable units.
It's come a long way and it's gonna continue and it's the speed of construction. We are in a housing crisis and we need to build and we need to build as quickly as possible.
Kelly: That's that's a perfect transition, I was hoping that maybe you could speak a little bit about how NRB has positioned itself with the Rapid Housing Funding Initiative from the federal government.
And that is an initiative that the King William Project that we alluded to at the very beginning, and that's a funding bracket that the project has qualified for. Could you speak or explain how you've positioned yourself with NRB to accommodate and meet the needs of this Rapid Housing Initiative?
Jackie: Sure. So I think most people in housing understand what the Rapid Housing Initiative is, but for those that aren't, familiar with housing, the federal government through the CMHC provided 2.5 billion for housing over a two, to three-year period.
So round one was completed, and round two is now being completed. They're looking at round three. There's a northern portion of it as well for Northern Housing, specifically more for First Nations groups and communities. But what we saw was an opportunity to provide housing in a very rapid fashion.
So the first round of the Rapid Housing Initiative was actually mandated to be modular. The second round was not so as the first round. We picked up quite a lot of business, obviously and we're able to secure the contract with the City of Toronto. We're into phase two of those builds now.
And those have been extremely successful. So I think the Rapid Housing Initiative is out there. I think it's gonna continue for some time, but CMHC has a whole host of different funding options that both municipalities, nonprofits, and developers can get into. And even, the region of Peel, I was on a call with them last week. They had a general call out to developers and they are providing more funding for people who are going to do more affordable. So they're trying to entice the development community to ensure that they are including more affordable units within their standard market housing.
And that's where I think we're gonna move next go from what we have been doing, which is a lot of the supportive housing into more of the market-driven housing. But it's not like we're gonna do one or the other. It's whatever the market is driving.
Kelly: It is very exciting and kind of development both because of all of this funding from the federal government, whether it's through the Rapid Housing Initiative or the CMHC co-investment funds. There are a lot of large-scale built-in-place developments that are being used with that funding incentives. But you mentioned that there's gonna be a lot more market-driven or like market scale developments that you're gonna be moving into as well. Do you see any energy efficiency kind of adaptations or requirements with that as well? Or is it just building housing conventionally and that's it?
Jackie: Yeah, I think, for us, we're gonna always try and be as energy efficient as possible, but I think there is a drive by the development community.
You know what? It depends on the developer and it depends on the municipality and their requirements as well. As an example, I think the Region of Peel is requiring net zero moving forward. And that's why I think actually it's really important that a lot of that CMHC money through the Rapid Housing Initiative has gone through down to the municipal level because then it's up to the municipalities to determine what it is that they want in their communities.
And sometimes it's cost driven and sometimes it's not. It just depends. But we are definitely seeing an uptick in either requirement for Passive House or the requirement for net zero. And that's something that we're working towards every day.
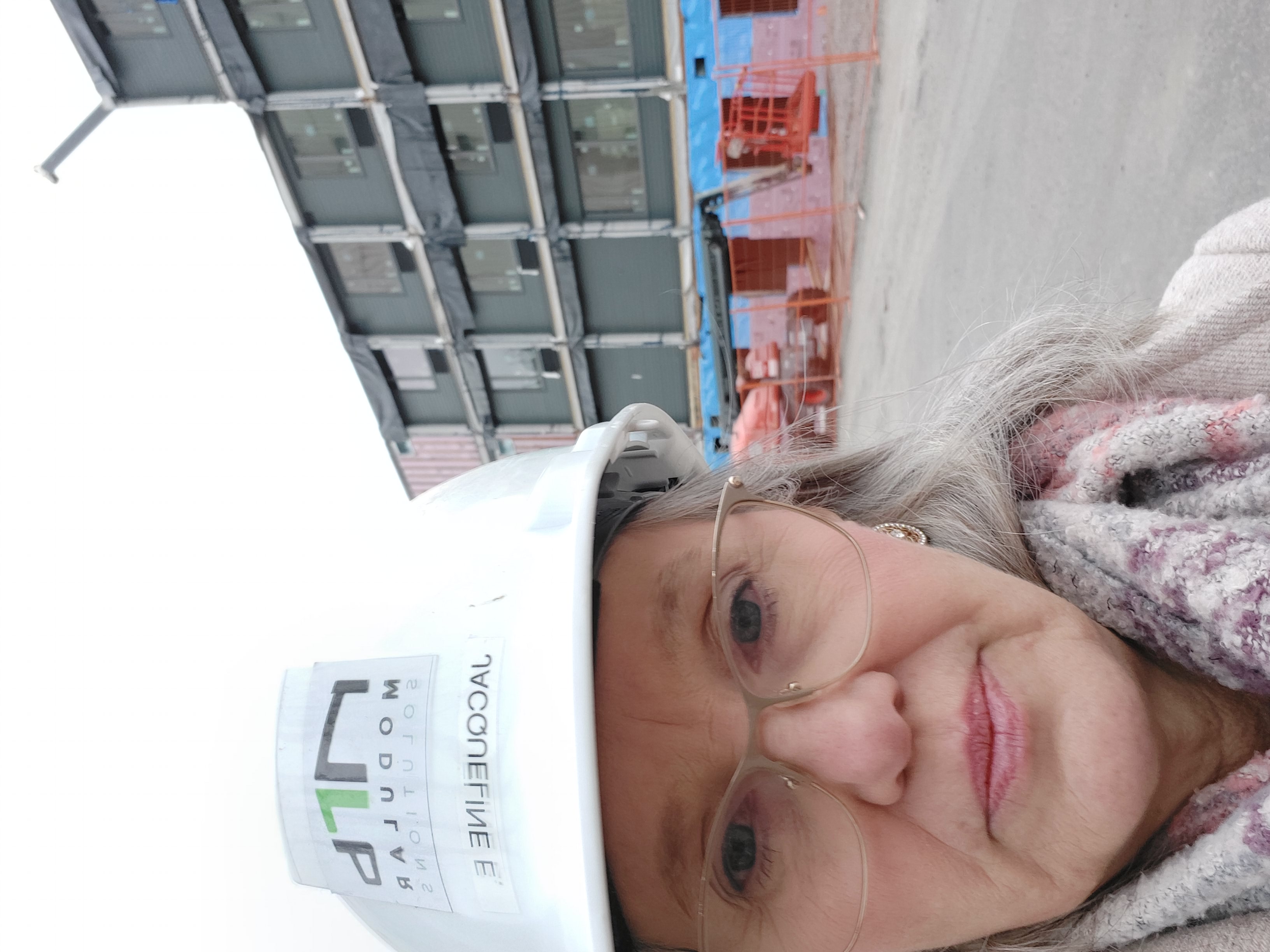
Kelly: So that's a good transition then back to the King William project in Hamilton that we're working with NRB and MSA architects with. So I wanted to bring everything back to this because the King William project is modular construction.
It's also gonna be achieving Passive House certification, and it's in the city of Hamilton which have a lot of Passive House projects underway. A few have been completed, and it really speaks to what municipalities can do when they have the capability to direct this funding as they need to.
But what I wanted to really pull everything back to, and to better understand Passive House and NRB, is to see has the King William project and its requirement for Passive House certification has been a driver for NRB to adopt Passive House as part of their structure or, a product offering or was there interest in Passive House before you won a project?
Jackie: I would say both. I know my colleagues in the east might not like me to say this, but the reality is that green building from the get-go has always been west first and pushed to the East coast. And whether we like it or not, that's the reality. So I would say that even though this will be NRB's first Passive House modular build east or west it's definitely not the first inquiry for Passive House.
And most of those inquiries have all been Western-driven. So as soon as we got this one in the east, all the guys in the west were very excited. Because it was like, "oh wow, we got one. We're gonna build it." There is a huge amount of interest. Yeah. And I think you guys are doing this every day.
You must see the massive amount of interest in Passive House.
Kelly: It's huge. Yeah.
Jackie: To me, having been involved in sustainability for a really long time, it's really simple, right? Passive House is not complex. It's not as complex as, LEED and some of the other certifications out there that go above and beyond the actual building.
And really if the focus is to try and reduce our GHGs, then putting a bunch more insulation in a building kind of makes sense, right?
Kelly: It's just a practical standard that, I don't know sometimes no disrespect to LEED or well, or anything like that cause they, they have an important focus on occupant wellbeing, but Passive House from like a building science perspective really nails it down and delivers on those reductions in energy consumption, improvements with our emissions.
It just makes the most sense when you look at it from a building science perspective. So it's always interesting to hear people in the industry have the same sentiment. Once they get into it and they understand and they get into a project, they're like, oh, it's always like they catch a bug and they can't let it go kind of thing. It's great to hear that from people.
Jackie: Yeah. I think that our operations guys are excited to get it going and get into the plant and start building. And I know that you've been working with them closely to make sure that we have our hole filler guy and as it goes through the...
Kelly: You got everything you need.
Jackie: I was just gonna say it makes complete sense right to do Passive House in a controlled environment. It makes sense to do it stick build as well but from my perspective, a controlled environment can really help ensure that everything is done the way it's supposed to be done.
Kelly: Yeah. That QA/QC process really benefited from having a controlled environment to build in. Gotta agree with that. Yeah.
Jackie: Yeah. I don't think most people recognize that as a mod goes through our plant that it goes from one station kind of thing to another. And we have our quality control guys that are great wandering around with their iPads and it can't move to the next station without them having gone through it and showing where all the deficiencies are and what needs to be done. So essentially by the time it leaves that factory, it should not have any deficiencies in it, including holes where there shouldn't be. And we are gonna do some air testing right inside the factory before it goes to the site. So that's exciting and that's new for us. So that's something that I think there's no reason why we can't continue to do for other projects.
Kelly: Absolutely, once you build the system and you integrate it into your process, there's no reason to not think with that methodology for your typical construction and to just, improve what your baseline is. So it's interesting and also fundamental to the program.
Jackie: Yeah. Our next I guess push is to try and figure out how can we do the envelope inside the factory as opposed to site-built. That's the next step how can we figure that one out?
Kelly: That's a struggle with Passive House built when we're looking at the insulation and the air barrier and everything, so
Jackie: That is a struggle. It is a struggle.
Kelly: A hurdle for every kind of prefab assembly when you're looking at Passive House is finding that. That connection back, I think if whoever does it is going to make a lot of money.
Jackie: Yeah, I know, we're working on it. (laughs)
Kelly: Awesome. So when you mentioned you got to like your QA/QC process that's inherent to like your modular construction and your process through your production line.
When you're looking at building to Passive House versus your conventional kind of process, do you foresee any challenges for, getting everybody on board with maybe some of the extra effort or some of the extra monitoring or even this fundamental change in construction?
Jackie: Honestly I don't think so. Because I think what's different about modular construction is that they're used to doing things a certain way over and over again. And they get good at that task, whatever that is. And so all we're doing is just shifting gears a little bit and showing them a new way to do something.
And I don't foresee that we're gonna get a lot of pushback. There was a lot of interest and that's why, we did the training, et cetera, which was really important for everybody to get on board. And I know that a lot of people went away to even understand what it was, right?
Because you asked people to come to training, but they don't really know what it's for. But there were a lot of people that actually went away and did their own little research on it and "what does this mean and how..."
Kelly: We had a lot of interest from the crowd that sat the training and just trying to understand the fundamentals to it all and I suspected the reasoning for a lot of their questions was so that they could take it away and better understand and then potentially apply it to the way that they're doing things now and to see what the transition and the changes would be for Passive House versus, how they do things now. So yeah, it was a great part of the process.
Now, you mentioned there just a few minutes ago about the training that you received for your team and for NRB. Now, I just wanted to preface that for those listening to that, this was a group training that the NRB team received as part of the King William project in Hamilton.
It was a requirement for the project to have the people who are gonna be working on it, both from a design standpoint and in the factory and production, to better understand what's required for Passive House when, we have to change kind of the mechanisms for how you build, maybe look at the fun the more fundamental principles of Passive House and how you can incorporate that and those requirements into your existing workflow.
So with Peel Passive House, we took on I think maybe 13 or 14 people from NRB. We sat through a sort of trades course to better understand how all of this would happen and how it would adapt any of the existing kinds of structures. But I wanted to better understand, when did training become a part of the conversation at NRB?
Was it a requirement for the project, or was it something that you were gonna eventually look on and undertake on your own to get, your team more up to speed and aware of what's required?
I was pushing for it right from the very beginning, because I know that if you get buy-in from people and they understand why it is that they have to do that, right?
If you're telling somebody it needs to be airtight, but they don't really understand why it needs to be airtight, but then you have the training and then they understand or they don't wanna make a mistake and drill a hole where they shouldn't drill a hole or get to the site. And, after we've spent, a lot of time, effort and money, looking at the envelope and then you stick a security camera on the outside of the building without thinking about how that's gonna be attached to the building you need people to really understand why it is that we're doing things the way we're doing it. It doesn't even necessarily need to be deeply involved in technical training for a lot of these people. It's just to give them an understanding of the overall goal as a team that we're trying to achieve.
Because in the end, it is a complete team process, right? From design all the way through to construction and occupancy. That chain can get easily broken if one link, doesn't get it.
Yeah, absolutely.
Jackie: Yeah, for us it was like right from the get-go. We need to have training.
I will say it's more of a discussion about when that training actually happens, right? Because you don't want it too early so that people forget by the time it actually gets to the plant, but you don't want it too late so that it's not actually applicable to the timing of the modules going through the plant. You gotta work through the training and figure out when. And especially for us, right? We had some design people in there. We had operations people, we had quality control people. I was there. So there was a whole gamut of people involved.
Kelly: It was a very diverse group when it came to the different departments within NRB.
So at the end of it, I was like they've got, people from sales all the way through to production here. So it's really a great yeah, as you said, a gamut of people to get the full kind of understanding for all aspects of your company and your structure, which I thought was a really great way to like interweave Passive House into that.
Andrew: Yeah, and I think I'll pick up, I think that your point about when the training happens is a very interesting and important question and getting it the timing right. And I think one of the benefits of how training has evolved is it could be in person, it could be virtual you can have pre-recorded, post-recorded stuff so people, even if you wanted early enough to influence the design, right? NRB's getting involved in the design. But then yeah, how is it affecting your production processes? That's gonna come later. But you need to understand that as well, anyways, to feed into the design. So that benefit of being able to do the training, but also having access to the videos, the material later on, for for a good period means you can go back to material and, okay, hey, we learned about this now I need to know something more specific about air tightness.
Okay. I can go to that section of the course and run with it, not retake it, but, watch it again now that I'm really applying it for this specific purpose.
Jackie: Yeah. I think the one thing that is significantly different in modular construction versus stick build is that we have shop drawings for every single one of our mods, right? So we will take the Revit file from the architectural file and flip that into our shop drawings. And those shop drawings are what we build from. So what we learn through the process of design has to get put into those shop drawings and executed in the operations side of things.
It is interesting because you would think the training really needs to happen at the very beginning, right? For the designer, whoever that architect is, whether it's us or MSA or whoever. But in reality, it also for us, has to be reiterated at that shop drawing stage to make sure that when they flip those drawings, there's no falling back to, "oh, let's do it the way we did it before." Yeah, I mean it's a process
Andrew: And in some ways, there is a similarity with traditional design, bid build with site builder cause you've got the design folks to need to understand it, Passive House. Then you've got the kind of construction management folks to need to understand it. They're the transition between design and construction. And then you've got the tradespeople on site actually doing it. And they have different needs and they're going to need to know at different times, right?
Jackie: Well, that's one thing, I will say that when you have a controlled environment, we do have complete control over our trades. They don't get away with anything. (laughing)
Kelly: There's no room for misbehaving.
Jackie: Yeah. And I say that with great love. But they're part of our team. They're integrated into our facility. It's not like a traditional job site where somebody could screw up and who knows who did it and when.
Kelly: Yeah. Everything is closely monitored. Yep.
Jackie: Yeah, the quality control guys know where you were and when you were there.
Kelly: Absolutely. There's a record of everything, which is great. And that's a unique nature that we like to see for Passive House too when we're doing that kind of construction is making sure that everything is documented and we can make sure that, oh, who put this hole there?
You've got a list, so and so was in this mod at this time, and there's a hole now.
Jackie: And a lot of photographic evidence, right? So for us, we have to have our CSA-277, which is our certification, right? It's our quality control, but it's also to allow us to complete a mod in the factory without full building inspectors coming in and looking at it.
And so yeah, there's everything documented just so that if the building department does call and says, we wanna see what's behind that wall in mod number 52 we have the ability to show them what is behind that wall. So there's the documentation that is required for certification is already built into our process. One would think that it would be fairly easy to get the certification. Let's hope it goes as well as, I think it's going to go.
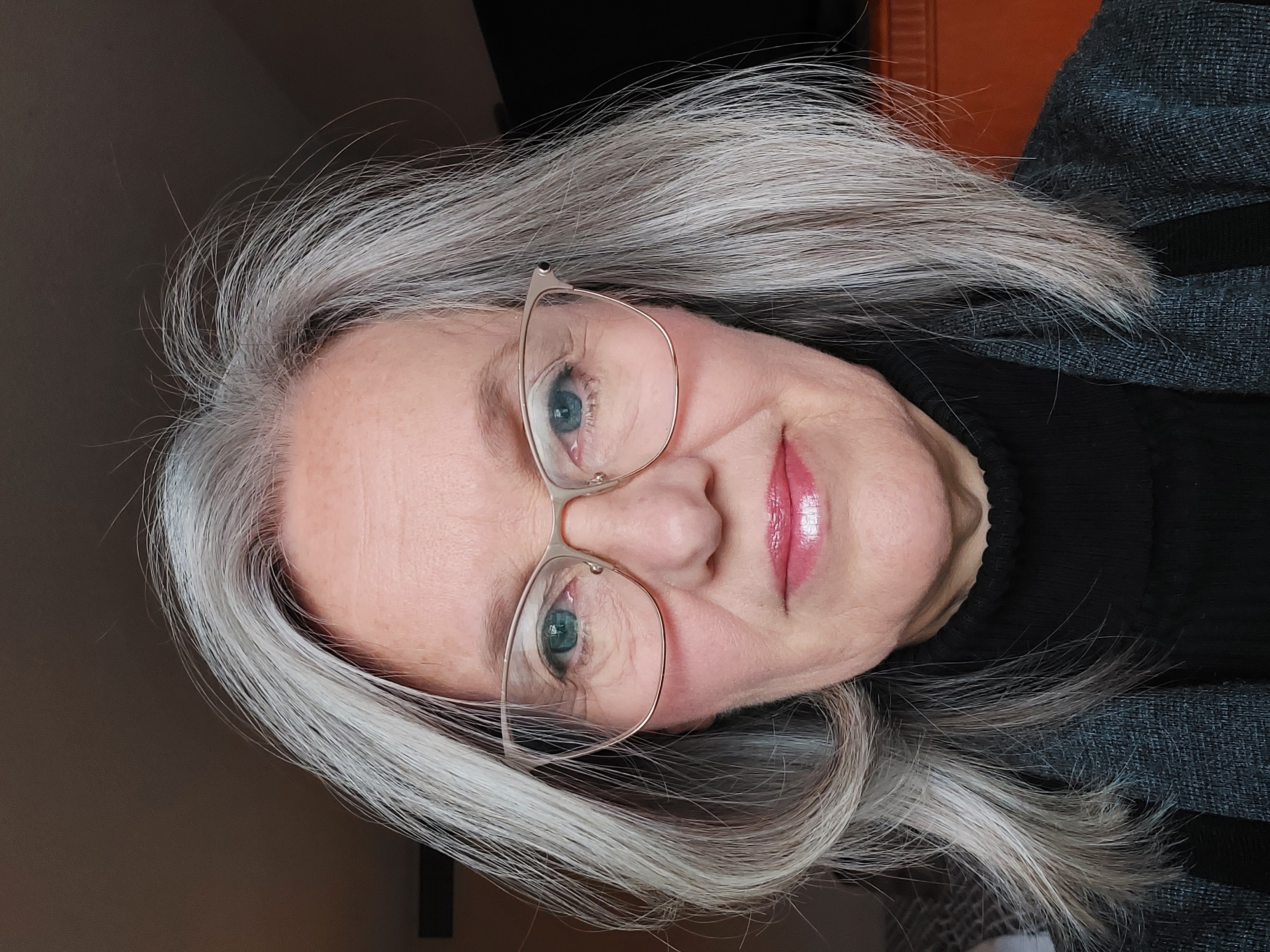
Kelly: I just wanted to round out today, so thank you so much for joining today's session. We really appreciate your unique insight both with modular construction and with Passive House.
I wanted to see if there's anything that you could share with us about what does the future hold in store for NRB and is there anything that you're especially excited about that you might be able to share with us?
Jackie: Oh, I just, I think we're gonna just keep on building. That is just the nature of what we do, and specifically, in the housing sector, the speed that we can produce just lends itself to where we need to go as a society, right? We just need to build more housing and we need to do more infill, lowrise type products in areas that we didn't even know we had.
Like the church parking lot, how many people are actually going to church now and do they need all those parking spaces? Can we put some housing in there? All those kinds of projects. That's where I think you're gonna see modular everywhere, but you may not know that it's modular.
Kelly: That's the unique nature of it that I really like. So just a kind of one more thing for you, were there any questions that we haven't asked you or anything that we haven't talked about that maybe you'd like to answer?
Jackie: I would say that there is a discussion around costing and I think that at some point, we do have to be realistic about how we discuss the cost of both modular and Passive House construction.
cause there is a cost to both. And I think that the more open and honest you are about it, the better we will all be off. And I remember when LEED first came out, there was a cost associated with LEED. Part of that was the learning curve for the architects. And part of that was just, people not understanding what it was that they needed to do.
But whenever we have a discussion around cost, whether it's modular or whether it's Passive House, it's always in comparison to what, right? What are you comparing it to? So if you're comparing a tier-one Toronto Green standard build to a Passive House built, that's one thing.
If you're comparing a net zero build to a Passive House build, that's a different thing. So what do you, what are you comparing it to? So I will leave it there.
Kelly: It's not always apples to apples when you're looking at it from that perspective. It's a fundamental part of the process. It's hard to compare the end result of a built Passive House to a built conventional construction. And the benefits that you get out of a Passive House are more than just the energy savings. So it's a hard thing to quantify as well when you're looking at it from like a user experience and the people who are actually living in these buildings, like their quality of life has greatly improved, and how do you put a number on that?
Jackie: Yeah it's true. And I think we've been trying to quantify that for many years, especially in the office sector. Even more so than that, the housing sector, which is a bit odd considering it's where we sleep at night. But we're still breathing,
Kelly: Yep. Some of us are better than others.
So it is generally than with the stream for like how Passive House has affected your day-to-day operations. So we talked a little bit about how we incorporate it or how you have worked to incorporate the Passive House principles and methodology into whether that's your QA/QC process, your production line, and even your designers and how you're preparing like your shop drawings and stuff. Has it been integrated already into your business model for when you're, proposing or you're looking for work to go to? Are you seeking out Passive House projects and proposing your solution with NRB Modular? Or how, have you looked for any integrations into your business model with Passive House?
Jackie: It's a difficult question to answer only because the builds that we are doing now that are going through the plant now have already been designed to a certain standard. And we build to whatever the standard is that the client is requesting. Having said that, though, we are implementing a sort of things that make sense from an environmental perspective that you should be doing anyway within our standard operations.
I would say though that the King William project is being used as a tool to go to market and say, we can do this. It is a possibility. If this is what you want, we can build it for you. It's like that old saying, if you build it, they will come. And, it's the same thing.
Honestly with net zero as well. Net zero carbon we're looking at a potential standard for that as well so that if the client comes to us and says, "can you do this?" then we have a solution for them.
Kelly: So have you seen an increased demand for Passive House or an increased awareness within, your existing clients out?
Jackie: For sure there are definitely RFPs out there that are coming out requiring Passive House or some standard that's much higher than we would typically have seen in the past. The RHI funding initiative did not have a really high energy requirement. It was 25% over the National Energy 2015.
And, that's still good. It's still good. It's just if you can hit 40, that would be better. And a lot of municipalities just go with whatever the requirement is for that funding. They're not reaching for more. Some municipalities are pushing that envelope because they say even though the funding doesn't require that, our own bylaws or requirements are asking for that. Just like the Toronto Green standard is getting ratcheted up. So are all of the other municipalities looking at their own energy requirements and changing those?
Kelly: Yeah it's an exciting kind of movement to see happen. And I always find whenever there's like a first step for one of these standards that comes out when you're looking at, don't, a TGS like Toronto Green Standard or any other municipality that's taking it on, like at West, they've got the Step Code in BC and the very first steps is always a bit of a shock for people.
Like a bit of a sticker shock. It's " oh, I have to do, 25% better than any CB" or like the energy code or whatever your local code is. And everyone's " oh, that's more insulation, that's more insulation." And then three years later they're generally used to that so that when the next kind of increase comes along and you've gotta build a little bit better and a little bit better it's nice to see that progression happen. I just wish that it would be a lot more stringent at the beginning because sometimes you just feel like it's just a bit of a wash when 15 or 20% here and there. It's just like, how do you quantify that and what is the end?
Jackie: Yeah. It does come back down to that old adage, and this will never be solved between capital expenditure and maintenance and operations expenditures.
And that is fundamentally an issue, right? Because there's no money for operations and maintenance. But then there's no money for capital expenditures either, right? So they blame each other for why we didn't do it this way.
It is getting better though. It's getting better.
Kelly: It's getting better and it's nice to see that the affordable housing sector has really been a push for Passive House standards generally. There are a lot more projects that we're involved with when it comes to these housing developments.
I always find, it's like when you're looking at these organizations that build social housing and historically they build, mediocre buildings, whatever the code minimums are at that point in time, whatever the most cost-effective systems that go into them are. But I always struggled with that because it's like they're building these low-cost buildings, but they're putting all of the costs of operations back onto the tenants to heat the buildings to run, their own hot water. And it's like these costs are only gonna increase. And you're asking people already in financial constraints to foot this bill when the building could be just generally built better. So having that kind of connection back to social equity for the people who are living in these buildings, to me is a fundamental part of the process.
You can't build a poorly built building and expect people who are already financially struggling to pay for heat, more for heat than people who are living in a Passive House building. It just doesn't make any sense to me, why we're putting that cost back onto these people who can't really afford any of their bills, to begin with.
So now they have to pay more. It just doesn't make any sense.
Jackie: Yeah. The way we have looked at housing has to change all across the board cause even. You think of First Nations communities in the far north and in the past, they may have had not very good quality construction projects just dumped on them and they're supposed to say thank you very much. When all they really want is good-quality housing.
Kelly: And it's such a fundamental right of life to have a quality place to call home.
And when oftentimes that's not the case, because, the funding's not there to even build it right to begin with it. It's just a tricky kind of process to be a part of it which is why the funding incentives from rapid housing with slight improvements over the baseline or the code and even, the CMHC Co-investment fund, there's a lot of play there with Passive House.
And the requirement that meeting Passive House certification gets you into that kind of bracket for that funding. And that is really key, I think, to this industry.
Jackie: Yeah, definitely the way they decide whether or not you're going to get that funding, the matrix, whatever they're using. The more energy efficient you can show that the building's going to be, the higher your score will be, and therefore you are much more likely to get funding. So that's something for sure. But I will say that one of the questions that I always ask people is who's paying the bills at the end of it?
So are you owning and operating the building and the heating and cooling bills are coming to you or are you downloading that onto the tenant? And unfortunately, depending upon that model there's a direct correlation between what kind of system they're putting in and how stringent those energy requirements are gonna be. We have to stop thinking about it that way because, if you look at it from a climate change perspective, it doesn't really matter who's paying the bills.
Kelly: No. Everybody is essential.
So I guess looping back into, Passive House affecting your day-to-day operations, do you have any predictions of what might happen with NRB and Passive House in the future?
Is it a standard that you're gonna look to integrate the market more generally to clients? Or is it something that's just gonna be, as required depending on the project?
Jackie: I think honestly it's gonna be a project to project and it's partly because we need to solve that exterior cladding issue.
Because for us, we really wanna put as much on the exterior in the plant as possible. Yes, we definitely are marketing it. Yes, there's a definite requirement for it. But that's a piece of the puzzle that I think we wanna try and solve. Everybody keeps telling me it's impossible, but I don't think it's impossible.
I really don't. I think there's a way we just have to figure it out. It may mean a hybrid type of model where we're porting portions of it on. But there has to be a way to seal it on-site. As a designer, I just feel like there's gotta be a way to do this.
Kelly: Yeah, absolutely.
So just to round out, all of our questions for you today Would you have any suggestions for anyone else, like any firms, whether they're modular, construction or pre-fabricated? Any suggestions for anybody looking to get into the Passive House industry?
Jackie: Other than calling Kelly and talking to you about how to do it?
Kelly: I mean that that can be number one on the list.
Jackie: Call Kelly or Andrew and have a conversation. That would probably be number one. And from there just learn as much as you can to understand the process cause it's the process you need to understand and then ensure that you are working with constructors who are gonna take it seriously and really value what it is that you're trying to achieve. And, make it sure that it's a team effort.
Kelly: All right, we've gone a little bit over our time, so thank you so much for hanging around Jackie. Again, thank you for your time. We really appreciate you taking some time today to sit down and share your experiences both with Passive Houses and with modular construction and even generally your experience in your career.
It's been really insightful to see your transition through, from flooring to modular construction, too, having a sustainability kind of personal incentive and your background with that is really impactful, I find. So I just wanted to say thank you so much for sitting with us today and sharing these experiences with both us and those who choose to listen to us.
So thank you so much.
Jackie: Thank you, and thank you for your training. It was awesome, and we're looking forward to having the build complete. And then we can go and raise a glass or something to the first Passive House modular build.
Kelly: That's gonna be a very exciting milestone.
Jackie, if people wanna reach out to you, how can they do
Jackie: They can always go to our website, that's one spa, which is NRB Modular. Or they can reach out to us via email, which is jacqueline.evans@dextera.com, that is our parent company.
Kelly: That's great. Thank you so much.